超临界 CO 2发泡 热塑性聚氨酯泡沫板的压缩成型Compression Molding of Thermoplastic Polyurethane Foam Sheets with Beads Expanded by Sup
Abstract
1. Introduction
2. Materials and Methods
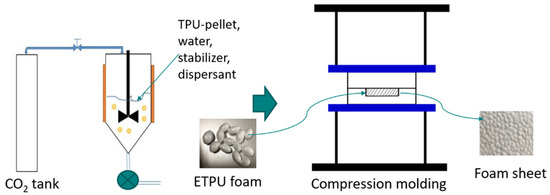
3. Results and Discussion
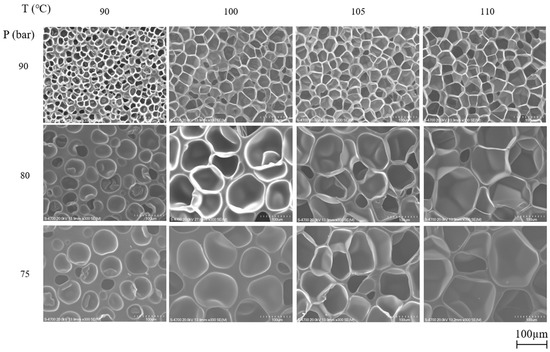
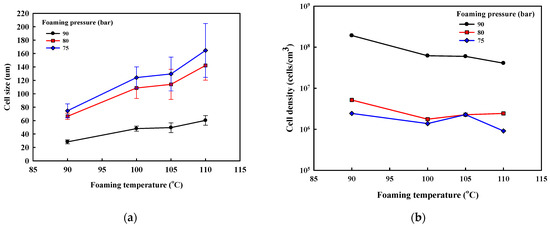
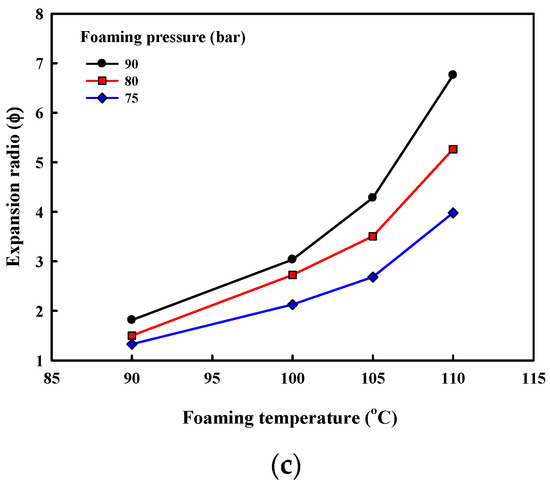
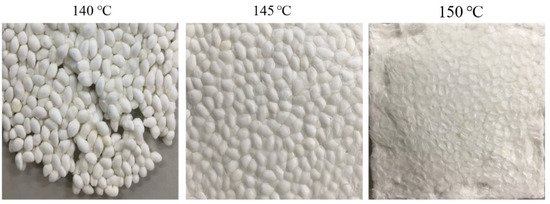
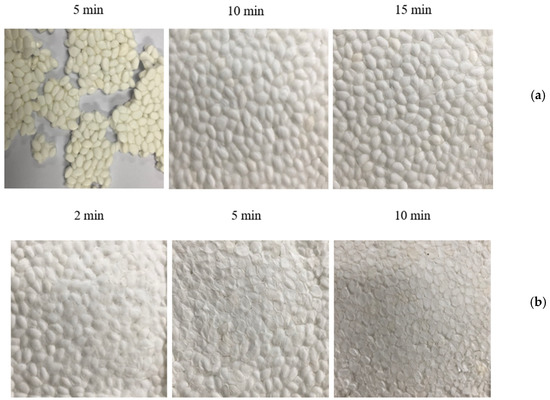
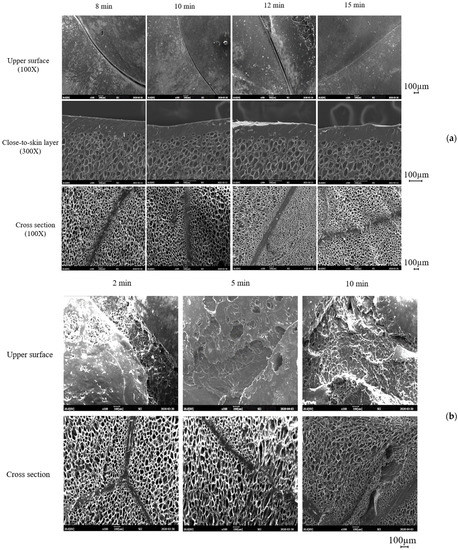
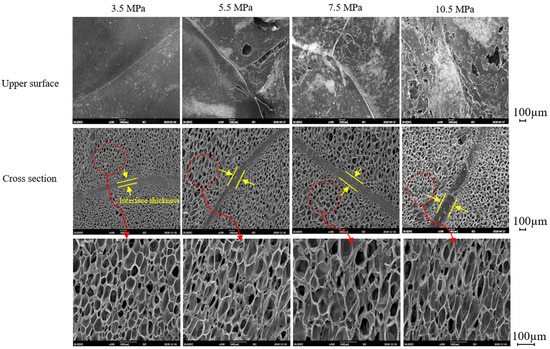

采用超临界 CO 2发泡工艺制备膨胀热塑性聚氨酯 (ETPU) 珠粒,然后通过压缩成型制成泡沫板。研究了发泡珠粒的泡孔结构对泡沫板性能的影响。发泡压力越高,泡孔数量越多,泡孔尺寸越小;在固定压力下,发泡温度越高,粘度越低,泡孔数量越少,泡孔尺寸越大,从而增加了 ETPU 的膨胀率。虽然与蒸汽箱成型相比,可以保持 ETPU 珠粒泡孔结构的加工窗口非常有限,但通过控制压缩压力和温度来实现珠粒表面的烧结,可以通过压缩成型 ETPU 珠粒来生产泡沫板。泡沫板的性能受珠粒膨胀率的影响,膨胀率的增加会增加泡沫回弹性,降低硬度,并增加拉伸强度和断裂伸长率。
关键字:
热塑性聚氨酯;发泡珠粒;超临界 CO 2发泡;发泡倍数;回弹性;硬度
图形概要
1. 简介
聚合物泡沫 [ 1,2 ]广泛用于轻质聚合物模塑产品。制造轻质聚合物模塑产品的典型工艺是 Mucell 工艺 [ 3,4 ]和珠粒泡沫工艺 [ 5,6 ] 。在 Mucell 工艺中,将化学发泡剂 [ 7,8 ]或物理发泡剂 [ 9,10,11 ]添加到聚合物熔体中,熔体在压力下通过模头或进入模具,并在挤出或注塑过程中冷却。在珠粒泡沫工艺中,使用已经发泡的膨胀珠粒 [ 12,13 ]或含有可发泡的发泡剂的可膨胀珠粒 [ 14 ]来制备泡沫产品。发泡剂加入到聚合物颗粒中,可以在聚合过程中添加[ 15,16 ] ,也可以采用高温高压反应釜将超临界流体状态的发泡剂引入到聚合物颗粒中[ 17,18 ],或者在挤出机中加入发泡剂到聚合物熔体中,通过控制冷却条件制备可发泡或膨胀珠粒[ 19 ]。
可发性珠粒最广泛用于聚苯乙烯[ 20 ],发泡珠粒则用于聚丙烯(发泡聚丙烯,EPP)[ 21 ]、聚苯乙烯(发泡聚苯乙烯,EPS)[ 22 ]和聚乙烯(发泡聚乙烯,EPE)[ 23 ]。发泡珠粒泡沫采用烧结工艺使用发泡聚合物珠粒制成,具有优异的绝缘性、耐热性、抗冲击性和能量吸收性。尤其是,EPP因其机械性能、低导热性和减震性能而广泛用于轻质汽车部件[ 24,25 ]。最近,人们对发泡热塑性聚氨酯( ETPU)的兴趣日益浓厚,因为它可用于制备柔软而有弹性的材料,并且在聚合过程中其性能易于控制[ 26,27 ]。这些热塑性聚氨酯泡沫是优异的柔性材料,具有高硬度、回弹性、优异的机械性能和动态减震性。在由发泡珠粒(尤其是 EPP)制造聚合物泡沫成型产品时,通常使用蒸汽槽成型[ 28 , 29 ],其中将高温蒸汽送入注塑模具,以物理方式烧结和粘合珠粒表面。此过程中的关键因素是在粘合珠粒表面的同时保持 EPP 的泡孔结构,因此蒸汽的温度、压力和停留时间是重要变量。随着发泡珠粒的研究和开发,关于发泡珠粒蒸汽槽成型的研究也已有报道[ 30 ];还报道了将热空气与蒸汽结合以使蒸汽均匀渗透,以减少因蒸汽变化而导致的成型缺陷[ 31 ]。蒸汽槽成型无疑是成型发泡珠粒的最佳工艺,但由于设备成本高,其普遍适用性有限,因此似乎需要研究制造成型泡沫产品的多种方法。
本研究采用压缩成型来丰富泡沫产品制造方法,因为它是聚合物加工中最典型且最便宜的制造方法。在不同的超临界 CO 2发泡条件下,由发泡热塑性聚氨酯 (ETPU) 制备泡沫板,并研究了珠状泡沫结构对泡沫板特性的影响。
2。材料和方法
本研究中使用的热塑性聚氨酯是 Dongsung Corp.(韩国釜山)芳香族聚醚热塑性聚氨酯 (TPU: 6175AP),其熔点为 150°C,比重为 1.055 g/cm3 ,肖氏 A 硬度为 78。实验室设计的高压釜(CRS,韩国安养)用于 TPU 发泡以制备 ETPU 珠粒。高压釜中加入 250 g 蒸馏水、100 g TPU、6.70 g 磷酸三钙(TCP,Sigma-Aldrich,Merck KGaA,德国达姆施塔特)稳定剂和 0.13 g 十二烷基苯磺酸钠(SDBS,Sigma-Aldrich,Merck KGaA,德国达姆施塔特)分散剂,然后用高压泵(CRS,韩国安养)泵入CO2 。为了获得超临界 CO2 ,将温度设定为 90、100、105 或 110 °C,将压力设定为 75、80 或 90 bar;将 TPU 保持在高压釜中 30 分钟,然后打开球阀快速将压力释放到大气压力以制备膨胀 TPU (ETPU) 珠粒。为了制备 TPU 泡沫片,将带有温度控制系统的尺寸为 10 厘米×10 厘米×2.0 毫米的模腔安装在压缩成型机(QMESYS,QM900A,韩国义王)上。通过将 15 克 ETPU 充电模具保持在 140–150 °C 和 3.5–10.5 MPa 下 2–15 分钟来烧结珠粒表面,然后在 4 °C 的水中淬火来制备泡沫片。图1显示了制备ETPU珠粒的发泡工艺和泡沫板压缩成型工艺的示意图。
图 1.用于制备发泡热塑性聚氨酯 (ETPU) 珠粒 的 CO 2辅助发泡工艺和压缩成型工艺示意图。
所有样品的密度测量均采用 ASTM-D792 的水置换法。使用扫描电子显微镜(Coxem EM-30,韩国大田)获得的显微照片测量泡孔直径 (D) 和泡孔密度 (N),从而表征在不同温度和压力条件下制备的 ETPU 珠粒的泡沫结构。膨胀率是通过使用电子密度计(SD-200L,加拿大安大略省沃恩)测量发泡前后颗粒的密度 ( ρ TPU,ρ ETPU ) 来确定的,然后使用以下公式计算膨胀率 (Φ)。
φ = ρ TPU / ρ ETPU
(1)
制备 5 个尺寸为 20 mm × 90 mm × 3 mm 的 ETPU 泡沫片材样品,以 10 mm/min 的速度进行拉伸试验。通过使用拉伸试验机(Lloyd LR30K,美国俄亥俄州克利夫兰)测量拉伸强度、模量和断裂伸长率与伸长率的关系,并使用肖氏硬度计(BS-392-A,广州安妙仪器有限公司,中国广州)测量肖氏 A 硬度,来评估制备的 ETPU 泡沫片材的力学性能。通过使用实验室制造的回弹仪,将一个重 0.486 g 的 5 mm 球从 41 cm 的高度落下(H o),并测量其反弹的高度(H),来评估泡沫片材的回弹性能;球的回弹率根据以下公式计算。
R = H / H o × 100(%)
(2)
3。结果与讨论
图2显示了在不同发泡温度和压力下制备的ETPU的SEM显微照片。图2测得的泡孔直径和密度以及图3所示的通过测量发泡前后颗粒的密度确定的膨胀比反映了发泡温度和压力对这些值的影响。从图2可以看出,在本研究采用的温度和压力条件下,ETPU泡沫具有闭孔结构。从图2可以看出,当压力较低(75 bar)时,泡孔未充分发育,泡孔间壁较厚,表明该条件不适合制备ETPU。泡孔尺寸随着压力的升高而减小,在90 bar时,泡孔直径为20~60μm,泡孔密度为108个泡孔/cm3 ,无论温度如何,它都可以归类为细泡孔泡沫[ 32 ]。相反,在 90 bar 以下,泡孔直径大于 100 μm,泡孔密度为 10 6泡孔/cm 3,是传统泡孔泡沫的代表。这是因为在较高压力下 TPU 中形成了更多的核,其中相同总量的 CO 2随后扩散,由此发生的膨胀形成相对较小的泡孔。在固定压力下,温度升高会降低 TPU 的粘度,从而导致泡孔变大和泡孔密度降低。膨胀率随着发泡过程的压力和温度的升高而增加,这表明它更多地取决于泡孔大小而不是泡孔密度。从图 3c中可以看出,本研究中获得的大多数 ETPU 的膨胀率一般低于 4,这是高密度泡沫的特征。然而,当发泡温度为 80–90 bar 和 110 °C 时,可获得中等密度泡沫,其膨胀率为 4–10;当发泡温度为 90 bar 和 110 °C 时,可获得最高膨胀率为 7。泡沫结构取决于发泡条件,这无疑会影响由 ETPU 珠粒制成的泡沫片材的性能。
图2.超临界CO 2发泡工艺 中不同发泡温度和压力下制备的ETPU的SEM显微照片。
图3.超临界CO 2发泡工艺 中不同发泡温度和压力下制备的ETPU珠粒的物理性质:( a )泡沫尺寸;( b )泡沫密度;( c )膨胀比。
图 4显示了成型温度对泡沫板结构的影响。泡沫板是在 105 °C 和 90 bar 条件下对 ETPU 珠粒进行 15 分钟压缩成型而形成的。从图中可以看出,在 140 °C 下压缩成型时,由于烧结不充分,所以无法制造泡沫板;而在 150 °C 下,珠粒表面会熔化,这表明,通过压缩成型制备泡沫板应在略低于 150 °C(TPU 的熔点)的一个较窄的温度范围内进行。图5显示了成型时间对 145 和 150 °C 下泡沫板形成的影响。在 145 °C 下,珠粒的烧结不会像在 140 °C 下成型那样在 5 分钟内发生,但会在 8-15 分钟内充分发生,并且不会发生泡孔变形。在 150 °C 下,当成型时间相对较短(2-3 分钟)时,可以形成保持珠粒结构的泡沫片材;然而,在较长的成型时间下,可以看到与在 145 °C 下成型的片材相反的片材表面的变形。图 6显示了在与图 5相同的条件下制备的样品的表面和横截面 SEM 显微照片。图 6a中在 145 °C 下成型的泡沫片材表面光滑,没有显示 TPU 的不规则表面熔融,但图 6b中在 150 °C 下成型的泡沫片材显示出不规则的表面熔融,因此导致表面的破坏性变形。在芯层和贴近皮肤的层之间似乎获得了相似的细胞形态。在两种条件下,珠粒之间的界面都会随着成型时间的增加而变厚,表明珠粒表面进行了有效烧结。虽然在145°C下成型时泡孔结构没有变形,但是由于熔融,在150°C时原始ETPU的泡孔会发生变形,并且成型时间会延长,特别是在发生界面烧结的珠粒之间的界面处。
图 4. 成型温度对 ETPU 珠粒在 3.5 MPa 压力下压缩成型 15 分钟的影响。
图 5. ETPU 珠粒在 3.5 MPa 压力下压缩成型时成型时间的影响,成型温度:( a ) 145°C;( b ) 150°C。
图 6.在( a)145°C 和(b)150°C 下成型的 ETPU 片材表面和横截面的 SEM 显微照片。
模压成型压力对珠粒烧结的影响如图7所示。随着压力的增加,珠粒之间的界面变厚,这可能会提高泡沫片材的物理性能;但是,随着成型时间的增加,可以看到泡沫表面的破坏性变形和界面附近的泡孔变形(图6)。因此,在3.5 MPa下模压成型似乎可以得到最好的泡沫片材。根据这些结果,ETPU泡沫片材的模压成型是可能的,但是与蒸汽箱注塑成型相比,可以最小化泡孔变形的温度和压力范围非常有限,因此需要精确控制成型温度和压力。
图 7. 压缩成型压力对 145°C 下 ETPU 珠粒烧结的影响。
通过对在不同条件下制备的具有不同泡孔结构的 ETPU 珠粒进行模压成型,在 3.5 MPa 和 145 °C 的温度下模压 15 分钟,研究了泡孔结构对泡沫板性能的影响,在此成型条件下,珠粒会发生烧结,并且泡孔的变形最小。图 8 显示了使用具有不同泡孔直径和泡孔密度的 ETPU 在 145 °C 下模压 15 分钟后泡沫板的 SEM 显微照片。在所有 ETPU 中,通过表面融合进行烧结已经很充分;当使用在低压和低温下发泡的 ETPU 时,珠粒融合形成的界面更厚,并且泡孔结构在模压成型过程中不会变形。
图 8. 在 3.5 MPa 压力和 145 °C 温度下压缩成型 15 分钟后制成的 ETPU 泡沫片横截面的 SEM 显微照片。
图9显示了泡孔直径、泡孔密度和发泡倍率对模压成型泡沫片回弹性能的影响。球回弹性能通常用于评价泡沫的回弹性能。与硬度不同,球回弹性能反映泡沫的瞬时手感,当泡沫的回弹性能差或能量吸收低时,其回弹性能也较低。回弹性能通常通过选择聚氨酯聚合中所用的异氰酸酯和多元醇来控制。但是,如图9所示,即使使用单一聚氨酯不同的球,也可以通过模压成型具有不同泡孔结构的ETPU(由在不同条件下发泡TPU获得)来获得回弹性能。球回弹性能取决于发泡倍率,发泡倍率越高,泡沫的回弹性能越高(图9),这表明与高密度泡沫相比,中密度泡沫具有更高的泡沫回弹性能和能量吸收能。在 75 bar 下发泡的 ETPU 泡沫板表现出相对较低的球回弹率(图 9),这似乎是由于低发泡压力下 TPU 的泡孔膨胀不足造成的(图 2)。理论发泡率可由泡孔体积(V g )计算得出,而泡孔体积又可由图 3中的泡孔数(N)和泡孔直径(D)计算得出,理论发泡率(Φ理论值)可由颗粒体积(V p = 1)计算得出,图 9中显示了该数据以及测量数据。它与使用发泡前后测量的密度计算出的实验发泡率(Φ)显示出相似的相关性,这表明考虑两个相互补充的因素——泡孔直径和泡孔密度——计算出的理论发泡率与泡沫板的性能相关。
������ = Nπ6���3五���=否���6德3
(3)
φ理论值 = (������+������) /������= 1 +������= 1 + ���π6���3���理论 价值=(五页+五���)/五页=1+五���=1+否���6德3
(4)
图9. 泡沫结构对ETPU泡沫片球回弹的影响。
图 10显示了制备的泡沫板的肖氏 A 硬度。与球回弹性能相反,由于泡孔直径小、泡孔数量少,膨胀率低的泡沫相对较硬;另一方面,膨胀率较高的泡沫硬度低,因此较软。在低压和 75 bar 和 90 °C 的温度下用 ETPU 发泡制备的泡沫板,泡孔膨胀不完全,其硬度值与未发泡的 TPU 板相似。这似乎是由于发泡条件不充分导致大部分 ETPU 未发泡。随着膨胀率超过 4,硬度几乎没有变化,表明在中等密度泡沫板(膨胀率 ≥ 4)的情况下,由泡孔数量和大小决定的膨胀率不会影响泡沫板的硬度,而在高密度泡沫(膨胀率 < 4)的情况下则会影响。
图 10. 泡沫结构对 ETPU 泡沫片肖氏 A 硬度的影响。
泡沫板的拉伸性能如图11所示。拉伸强度和断裂伸长率随发泡率的增加而增加,但模量降低。由ETPU珠粒在相对较低的压力和温度下发泡制成的泡沫板具有较厚的泡孔壁,因此发泡率较低,由于未发泡部分的模量较高,施加的拉伸力很容易在珠粒之间的烧结界面处破裂。由发泡珠粒制成的泡沫板的拉伸强度取决于珠粒之间烧结界面的失效和珠粒内部泡孔的失效。当压缩成型条件不合适且烧结不充分时,珠粒界面处的失效预计会导致非常差的拉伸强度,但在适当条件下加工的泡沫板的机械性能预计取决于界面或泡孔的失效,具体取决于泡孔结构。图 12显示了本研究中在最佳压缩成型条件下加工的泡沫板的拉伸试验断裂表面的横截面 SEM 显微照片,可以看出,界面和孔隙处都会发生失效,其相对程度取决于所用的 ETPU。由低发泡率珠粒制成的泡沫板会在珠粒-珠粒界面处失效,而由于发泡压力和温度较高而具有较高发泡率的泡沫板会在孔隙处失效,从而产生较高的拉伸强度和断裂伸长率。也就是说,高发泡率珠粒中的闭孔结构吸收了拉伸试验中的能量,而不会在界面处失效,直到最终失效的是孔隙而不是界面。根据这些结果,似乎使用中密度泡沫珠粒而不是高密度泡沫珠粒更有利于通过压缩成型制成的泡沫板具有足够的机械强度。
图 11. ETPU 泡沫片的机械性能:( a ) 拉伸强度;( b ) 断裂伸长率;( c ) 杨氏模量。
图 12. 拉伸试验中 ETPU 泡沫板断裂表面的 SEM 显微照片。
4。结论
研究了发泡压力和温度对发泡TPU泡孔形成的影响,以及将制备好的EPTU模压成型为泡沫片材的可能性。研究了发泡珠粒结构对模压成型泡沫片材性能的影响,得出以下结论。
本研究中使用的 TPU 在 75-90 bar 和 90-110 °C 下发泡时呈现封闭的泡孔结构,并且可以制备具有细泡孔和/或常规泡孔的多种泡沫结构的 ETPU 珠粒。在较高的发泡压力下,会形成更多的核,泡孔尺寸会减小,从而导致更高的膨胀率,而在固定压力下发泡温度的升高会影响粘弹性,从而增加泡孔尺寸并减少泡孔数量,从而降低膨胀率。已经证实了压缩成型 ETPU 以制备泡沫板的可能性,但在烧结 ETPU 珠粒期间,EPTU 中的泡孔结构不会变形,从而获得泡沫板的加工窗口非常狭窄。ETPU 的膨胀率会影响泡沫板的性能,膨胀率越高,硬度越低,因此回弹性越高。发达的泡孔结构还有助于提高机械性能,例如拉伸强度和断裂伸长率。
Vg=Nπ6D3">